The challenges of the current market require the constant reduction of the time to market. Thanks to the 3D printing, Nidec Sole Motor Corporation has succeeded in reducing it by a good 5 times. 3DZ has supplied the printer that has become part of their instruments.
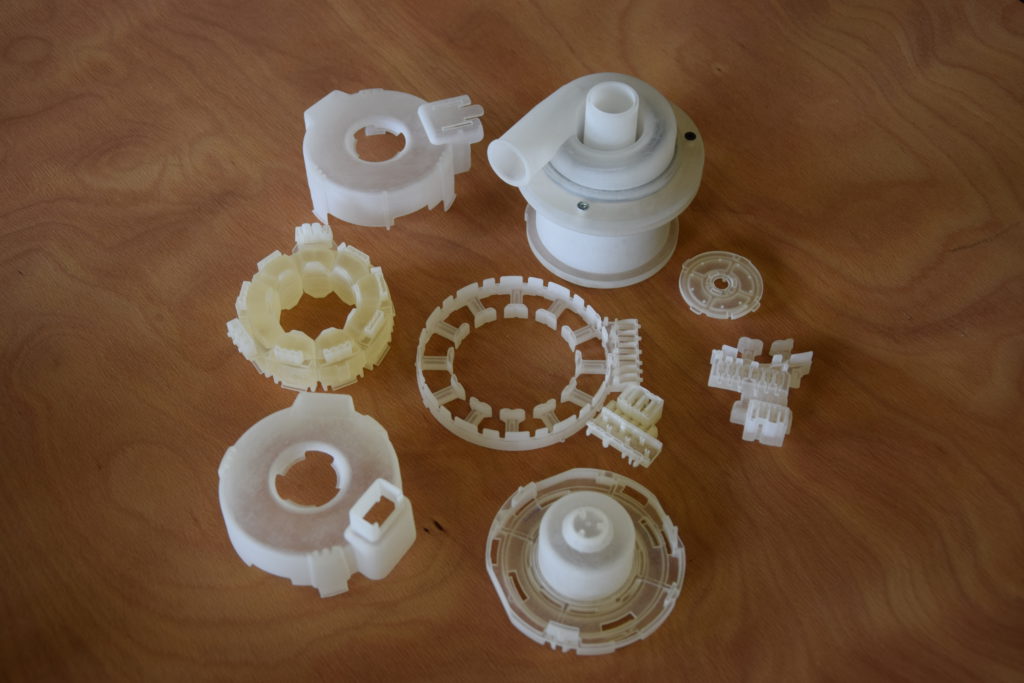
Established in 1973 by Shigenobu Nagamori, Chairman of the board, president and CEO in charge, Nidec Group is one of the main producers of electric motors in the world. With headquarters in Kyoto, it is listed at Tokyo and New York Stock Exchanges, it reaches a turnover of about 7 billion Euros with more than 100,000 employees in over 230 companies spread in 32 Countries. It offers several motor typologies, from the smallest ones dedicated to computers, portable phones, CD and DVD readers with fractions of watts â up to the biggest ones for âoil and gasâ plants featuring 45MW.
The business unit Nidec Sole Motor Corporation srl (NSMC), with head office in Italy, in Pordenone, is the company that inside the Group designs, produces and markets motors for household appliances such as washing machines, dryers and dishwashers. Constantly committed to the research of motors with high technological innovation, especially concerning the aspects of improvement of energy performances and noise reduction, the company is highly focused on the use of eco-consistent materials and the development of recyclable products.
The research and development department is headquartered in Pordenone; productive factories are located in Italy, Hungary, Romania and China and they supply customers â i.e. the primary household appliance manufacturers â prevailingly in Europe, North America and China.
A fundamental phase for the company is the prototype testing, whose results will start up the production or will determine eventual project modifications; fundamental, in this stage, is reducing the time that passes from the devising of a product and the implementation of the prototype to be tested. Precisely in this phase, the 3D printing is proving to be a precious ally.
The research and development sector of Nidec is subdivided by product applications: motors for washing machines, dishwashers and dryers; each platform has a dedicated team of engineers.
When and how the 3D printing has gained access to the company is explained by Alberto Grava, platform manager for the motors for dryers and the new applications, who follows projects with his team starting from the specifications demanded by customers. Not only what concerns white goods â then washing machine, dishwasher and dryer –Â but also the new applications outside the white good ambit such as motors for suction hoods or for domestic heating.
Grava precisely confirms how much the âtimeâ factor plays a fundamental role for Nidec. âThe market competitiveness has always called for the development of new solutions in very short times; therefore historically the rapid prototyping has been a requirement for the implementation of prototypes and the approval of solutionsâ.
Inside Nidec there was, and it is still present, a toolshop dedicated to the implementation of prototypes for development purposes but they had always missed the competence for the prototyping of plastic components, constantly outsourced to external suppliers. The will of shortening times and of âintegratingâ a specific competence for the implementation of plastic components has led to the decision of analysing thoroughly the potentialities of the 3D printing.
The specific step was getting in touch with 3DZ, authorized reseller for Italy of 3D Systems, and specifically with Gianfranco Caufin, one of the companyâs founders and current co-owner of Treviso headquarters. âNidecâs target consisted in providing autonomously for the printing of prototypes on which carrying out functional tests â confirms Caufin â and this request gave birth to a dialogue phase between the company and 3DZ to understand what were the most suitable technique and printer for its needsâ.
After the theoretical discussion, they proceeded to practical tests. Nidec has then provided 3DZ with the CAD results concerning some of its components, which 3DZ proceeded to implement with various printers: the various prototypes have been then submitted to the company so that it could evaluate their characteristics and examine the solutions better complying with its requests.
The choice fell then on ProJet 3510 HD by 3D Systems that, as explains Alberto Grava, âproved to be winning from the technological and economic point of viewâ. It is a printer that creates precise and resistant plastic parts for functional tests, aesthetical and design evaluations, rapid manufacturing, rapid tooling and much more. The printer, based on the Multi Jet Printing technology, produces items with maximum sizes of 298x185x203 mm, with a maximum resolution of 750x750x790 dpi and layer thickness up to 32 ÎŒm. Concerning materials, a broad range of materials from the VisiJet category is available for ProJet 3510 HD and various printing resolutions are possible, too; the support material is the VisiJet S300 wax, which has the characteristic of being easily removed.
After the purchase, 3DZ provided for the installation, testing and calibration phases of the printer and then the training activity of Nidec technicians, both about the machine use and the treatments to be carried out on products after printing.
What is the current use of the printer, in terms of products and frequency? Alberto Grava further explains: âThe application fields of the printer are the most various: we range from the implementation of either impeller-involute groups for the hydraulic testing of pumps for dishwashers or blowers for HVAC to the realization of mockups for overall dimension, conceptual or process testing up to the creation of components for functional prototypes like for instance connectors and supports. Since the installation, occurred slightly more than one year ago, we have used ProJet 3510 HD twice a week on averageâ.
Concerning the advantages, there are no doubts about the positive repercussions that the companyâs adoption of the printer has had on the time reduction. âThanks to the 3D printer, we have decreased the lead time by over five times and therefore we succeed in very short times in âtouchingâ the designerâs ideaâ adds Grava. âFor the most complex models, now we print one solution at a time, we test it and we launch the printing of the optimized component after some performance checks, notably reducing the quantity of tests to be executed. Previously, in fact, without the printer and having to turn to external suppliers, we simultaneously ordered some variants of the component but not always, anyway, we reached the target at the first loop, therefore needing a new order of items and a new validation courseâ.
A time convenience that makes the economic profitability calculated in the immediate term less important. âIn terms of cost of the component (raw materials and labour for the finishing) we have not noticed an evident economic convenience but the advantages in terms of time, autonomy and product control, even if they are hardly measurable, are clear. More precisely, in fact, the global spending for the prototyping of components has grown but due to an increment of prototypes. Relying on the in-house 3D printing technology, now we feel âless constrainedâ and, in a sort of virtuous circle, some ideas that previously would not have sprung from the mathematics of the 3D model, now can be practically implemented, just because now âit is easyâ.â
The satisfaction is clear, and it is then natural that Nidec already hypothesises an increment of the printer use and of the 3D printing technology. As Grava confirms. âWe will certainly increase the printer use, extending its application also to other business divisions, such as the quality for the implementation of fixing templates for dimensional measurements or for the control of line equipmentâ.
What does Nidec expect from 3D printing? âThe 3D printing of plastic materials at professional level will increasingly take hold in companies, with the complicity of the decrease of the necessary investment to acquire a high-definition printing quality. I expect an improvement of the mechanical performances of plastic printing materials and a decrease of the investment for the 3D printing of metal materialsâ. The forecasts and the expectations of Alberto Grava mirror the positive experience they are living in Nidec: they have just to follow the evolutions of technology and its applications.