Since 1969 FISE Spa (NO) has been leader in the sector of the manufacturing of «made in Italy» electric motors, for the industry of high-end household appliances. An integrated production cycle, customized solutions and all-round after sale service for all kinds of applications are its stronghold.
After starting seventy years ago as subcontractor for various household appliance brands, the company owned by Boccola family is today a technologically advanced, neatly green reality, always willing to collaborate with Italian and foreign companies for the development of new products to be released on the market. Currently, at the head of FISE, at the side of the President Luciano Boccola, there are his daughters Daniela and Silvia, respectively CEO and sales manager. We ask precisely the latter to tell us the growth and the evolution of the family-run company and what strategies have been deployed in over 50 years of activity to rank always at the top, on both the Italian and the international market, developing know-how, 100% Italian quality and an all-round integrated manufacturing.
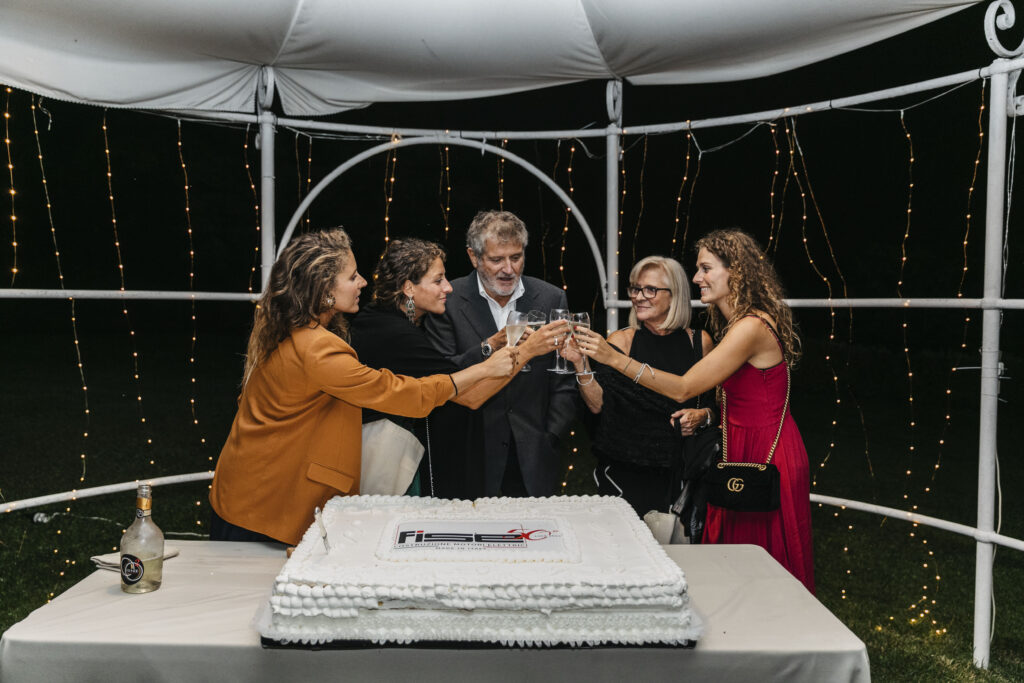
Can you tell us briefly the history and the mission of your company?
Our company has always focused on the production of electric motors.
In 1946, precisely my grandfather Daniele Boccola founded Elettromeccanotecnica Boccola in via Soffredini in Milan, but at the end of the Sixties the entry of my father Luciano transformed the company into what is still the current reality.
FISE Spa is a joint stock company, specialized in the manufacturing of AC/DC commutator electric motors, DC permanent magnet motors, brushless motors with or without integrated electronics and it offers innovative product solutions to the market, relying on a fully integrated production process. Our highlight? Certainly, all-round know-how, at 360 degrees, implemented with much fatigue along the years. This allows us to produce standard products, but also to manufacture fully custom products in conformity with customers’ requirements.
From the beginning to the end, in fact, the manufacturing process is faced in integrated manner, to succeed in delivering motors in short terms. The integration of the whole production process allows us to be flexible and to satisfy the various market requirements.
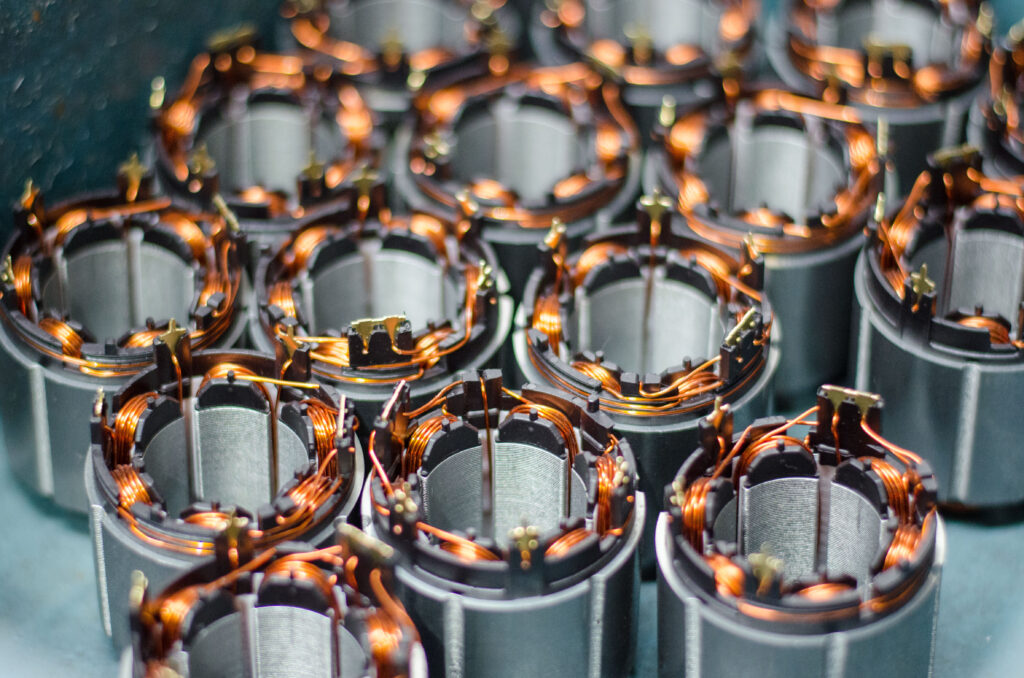
Whom do you address?
We address B2B customers: producers of small appliances, especially high-end models, such as vacuum cleaners, hairdryers, hand dryers, gate openers, automation, robotic lawnmowers, whirlpools, vending machines, mixers, coffee machines, pumps … the range of consignees is broad indeed. We offer our customers not only the motor but we give also an engineering support and wide-ranging service: we manage each phase, from the motor design to its final implementation.
How is the motor production organized?
Our manufacturing site, where we engage about 80 workers, takes up a surface of 27,000 square metres, of which 18,000 covered. We have a photovoltaic plant with which we produce almost 70% of our requirements. We have organized various in-house divisions that allow us to keep each motor manufacturing phase under control.
The Turning department, qualified for the production of precision small metal parts (shafts, hollow shafts, tubes, screws and so on) where, with state-of-the-art NC lathes, we produce small and medium batches of high-precision products with the most complex shapes. In this division, four grinding machines carry out the finishing of components after the first turning machining.
The Shearing division, where we produce sheared small metal parts for deep and very deep stamping. We shear different materials: various alloys of aluminium, brass, steel and stainless steels, according to customers’ demands.
In addition to shearing small metal parts, we also in-house blank rotor and stator laminations by using progressive dies.
The feather in the cap is a fully automated winding division for rotors and stators, to manufacture large volumes.
A further division is Moulding. It works at the technical moulding of plastic components for the most various departments. In this department, we have also prearranged two presses for Zama moulding.
Inside the company, we can rely on a forefront toolshop, which designs and manufactures machines and production lines, having all state-of-the-art NC machine tools at disposal. The same performs the tool maintenances and intervenes for the machinery arrangement, when necessary.
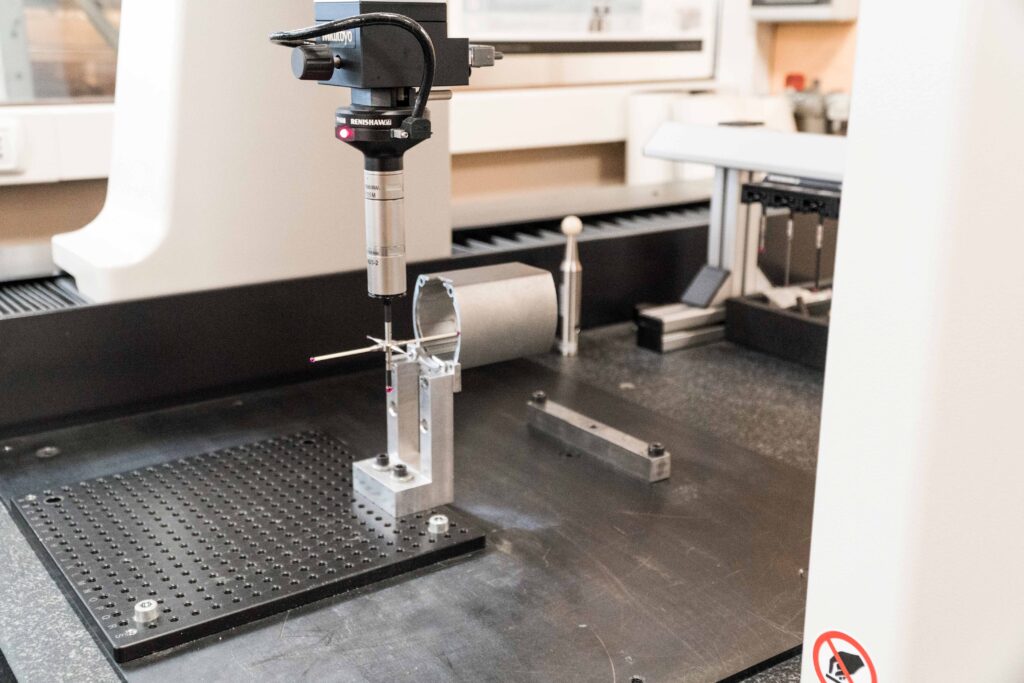
We have a centralized Quality Control Office, which takes care of all corporate divisions with control plans of production and process start. We are equipped with a conditioned metrological room, with controlled temperature and humidity, with Japanese forefront machines, CMM and VMM Mitutoyo, with which we control both production starts and the components of tools and machining operations.
Finally, there is the Assembly department, where we assemble and test motors.
Integration certainly represents an advantage: we are flexible and faster in answering to market demands but, on the other hand, we know we must avail ourselves of sound know-how and specialized team.
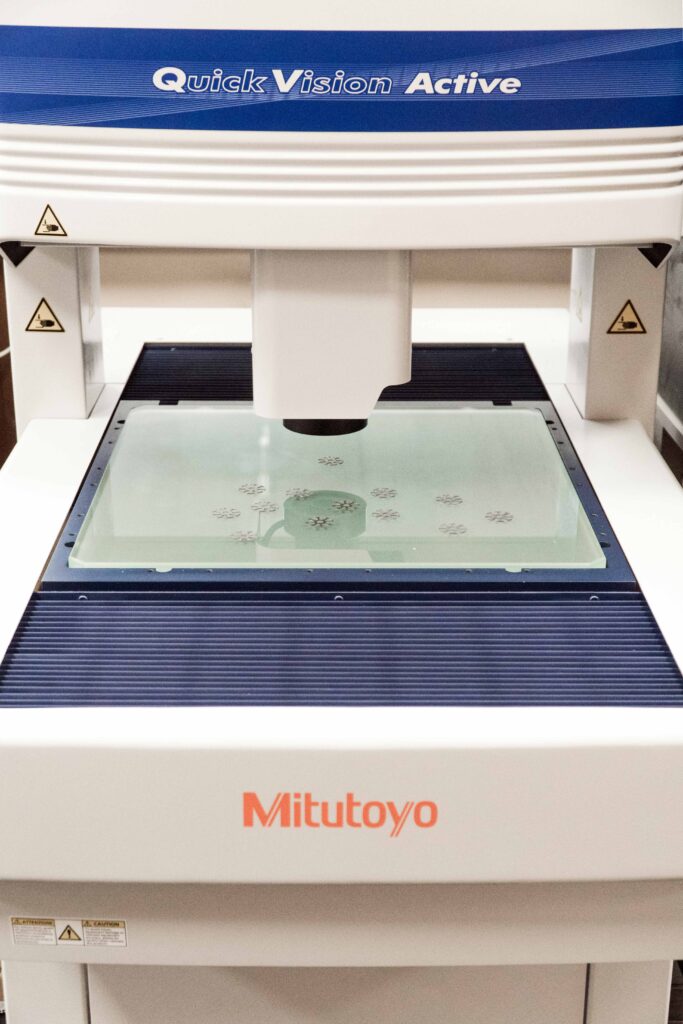
What is your company’s vision?
Fise vision consists in designing and manufacturing made in Italy electric motors according to a vision of innovation, environmental sustainability, energy efficiency and unceasing improvement, to be able to satisfy the demands by a constantly evolving market.
What innovations have given an important turning point to the business?
For a dozen of years, FISE has focused its efforts on the design and production of brushless/digital motors: brushless motors, for which we design also the electronic control board.
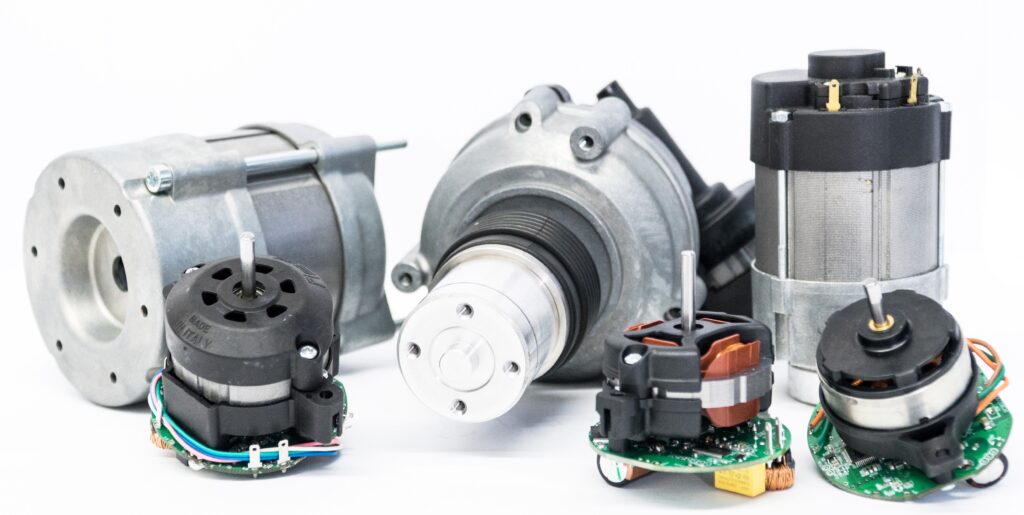
What are the highlights and the applications of the brushless motor?
The advantages they offer, in comparison with brush motors, include higher energy efficiency (they are motors with very high performance), a longer duration (more than the quintuple than the life of commutator motors), in perfect conformity with our attention to environmental sustainability and, especially, they imply a lower pollution, due to the elimination of brushes from the motor and to the possibility of using the appliance longer without having to replace it.
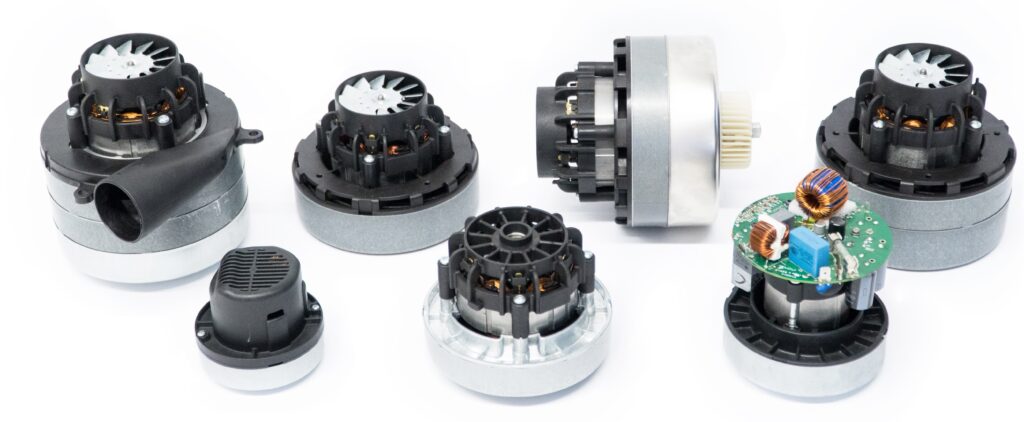
What is the advantage of having an in-house electronics Laboratory?
With the electronics laboratory, we try giving an additional service to our customers, who know they can turn to us for the implementation of their electronic boards. It is a further integration to our verticalization.
Inside it, we can follow the whole hardware and firmware development of electronic boards, which allow piloting brushless motors.
At the head of this office, there is the engineer Giuseppe Borrello who, thanks to years of expertise gained not only at Fise, can coordinate two laboratories, electronic and electric. In these laboratories, we conceive the designs of our motors and of our boards, and we carry out the drafting, the bills of materials, as well as performance tests, stress tests and emission tests.
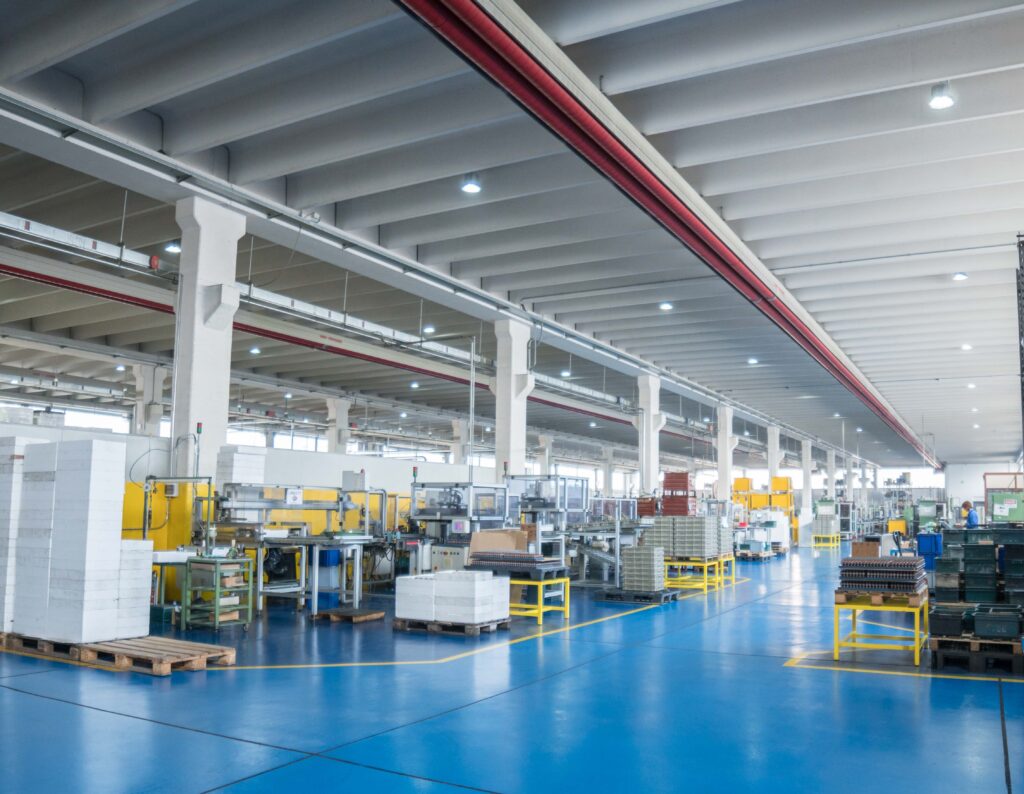
How are you getting ready for the future, then?
In the last two years, we have designed and manufactured two fully automated and robotized lines for the manufacturing of rotors and stators for brushless motors, where we will be able to produce all existing platforms and the new demands by customers: they are in fact multitasking lines and no longer single-product, with fast tooling.
In addition to investments in new machines and manufacturing lines, we have invested in the control of our reality’s productivity and efficiency. Therefore, we have introduced a MES system, as interface of all machines, to have in real time data and information about their operation and to be able to calculate the efficiency of each of them. The target is measuring in real time machines’ performances and immediately intercepting eventual anomalies. The system also allows monitoring the qualitative level, maintenances, the product traceability, from the incoming of raw materials to the output of the finished product.
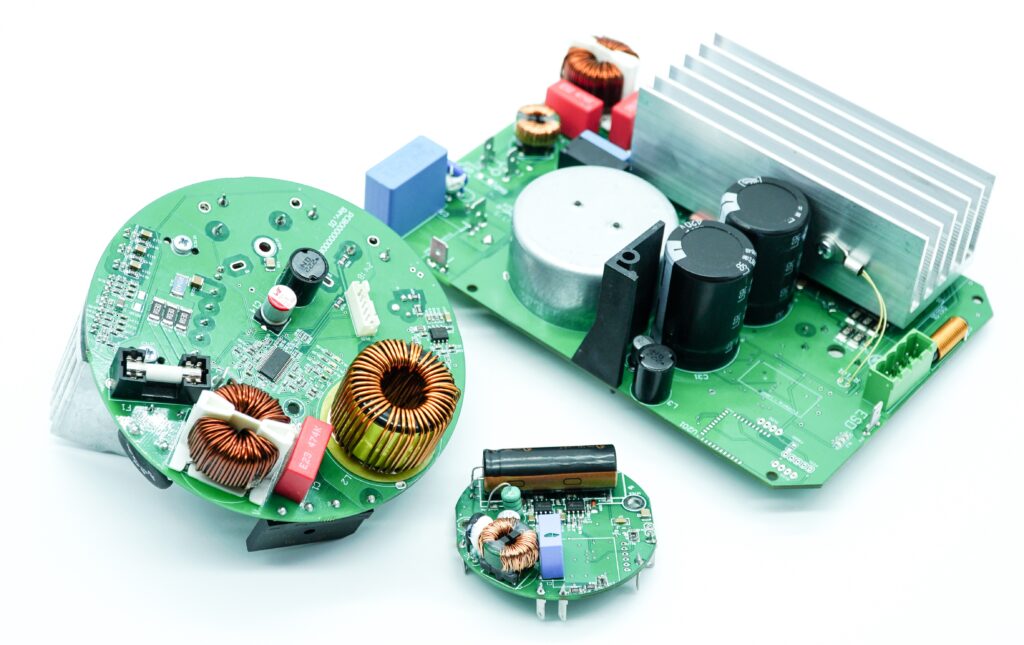
What difference does the made in Italy quality of a motor make and how do you communicate it?
The made in Italy has still a strong appeal for both Italians and foreign people, because it is a brand that speaks for itself and, associated to a product, means well-done and with guaranteed quality.
Staking on quality, on sustainability and service. This is the trump card that companies that make the real made in Italy their essence must play to compete on today’s global market, without surrendering to the price war against Asian companies. «Our company bets on innovation and the capability of offering customized products, fidelizing customers as much as possible and always ensuring excellent service levels.